
Every year Lenovo has a corporate event with a lot of very important clients. They are one of the world’s largest computer vendors and this year they wanted their exclusive invitation to be something memorable. Senior Artists Frank Ling and Ben Friesen recently delivered just that.
The request was for something that people would want to keep long after they needed to. It would also be great is the item transformed in some way. This post documents the entire process from brainstorming to the final touches.
In all the project took about 5 months to bring to life and everyone was thrilled with the final product. Enjoy this behind-the-scenes look at the entire process.
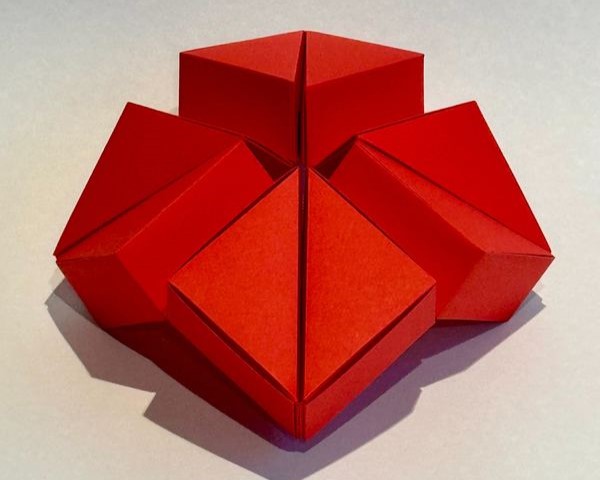
1. Brainstorming
Once the Taro’s artists received the request, they scoured the origami world for interactive and exciting models. Below you will find images of 4 of their favorites to use as a starting point.
First there is the origami firework model. This connected collection of 12 identical units has just enough play in it for people to twist it inside out. This creates a mesmerizing pattern of explosions that can repeat indefinitely.
Second was an version of an origami puzzle box. This version has 7 unique origami shapes that, when solved, fit exactly into a 3X3 cube.
After that the client was shown an origami modular ball. This particular model is by Ekaterina Lukasheva, and does a great job of creating spikes while holding together.
Lastly they presented a flexicube model from the David Brill. This model uses 8 origami blocks which fold around like the traditional children’s toy.
In the end, the client loved the last idea and the Taro’s Origami team got to work building a brand new model using it as inspiration.
2. Testing
For this phase, Frank Ling was able to completely deconstruct the origami model and create a facsimile in papercraft. To begin with Frank started with a 1 by 2 block, but as it turns out, one of the important identities of the Lenovo brand is that the logo is on a 1 by 3 ratio. So with that in mind Frank changed all the proportions, and in the process also found a way to make it easily replicatable on the Taro’s machine scoring tools.
3. Refinement
Once the basic shape was figured out and a prototype was sent off for the client to play with in person, the details of the model were refined. First there were changes to the joints to make sure the were stronger, and then Ben and Frank also played with different patterns to add to different sides. They were based off some neural network images from previous Lenovo corporate branding.
4. Production
The last touches for the delivery was providing a fancy box and holder to present the model. The team had custom shaped magnetic enclosure boxes made and then Ben jumped into full production of the final models. While Ben made the models, Frank started work on a triangular platform for the model to rest on. This made sure the model was presented as a monolith and would open up to reveal the Lenovo logos, as requested. After a few iterations, everything was finalized and everything was assembled. In all more than 160 blocks and 20 finished flexicubes were created, and production took about 3 weeks.
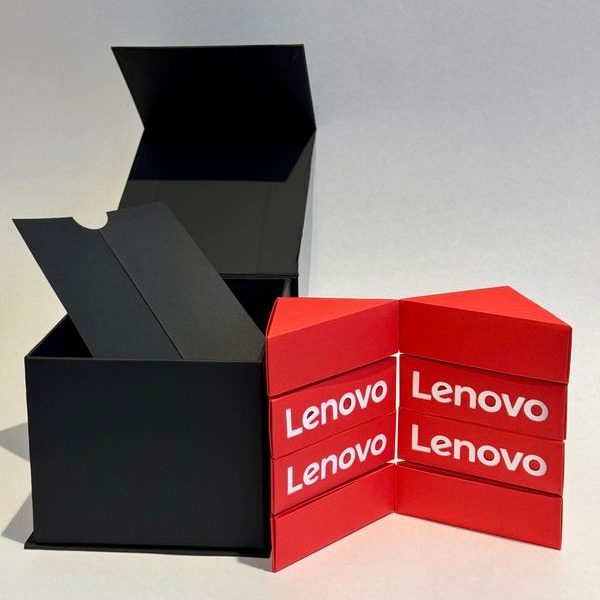