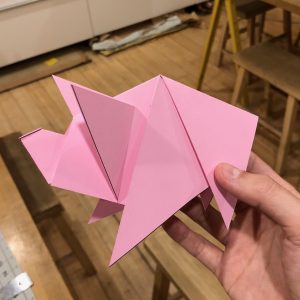
This was the traditional pig model picked for the campaign
Every year for the Chinese New Year companies find new ways to incorporate the zodiac animals into their advertising campaigns. This year Taro’s Origami Studio was contacted about creating some life-sized origami pigs for the international display campaign for Sandro Paris, the luxury fashion brand. Sandro requested over 75 pigs total in various sizes from a few inches to over 4 feet. They were also interested in shipping these pigs all over the North American continent, and making them all in a very specific shape of pink. This created a slew of very exciting challenges for the Taro’s Origami team, and they got to work right away.
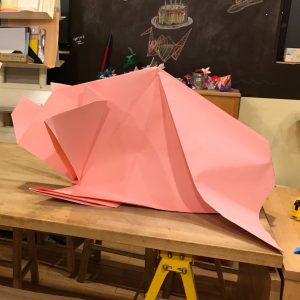
This was the first attempt out of paper
The first challenge to overcome was deciding on the materials for such a large project. Sandro was initially interested in a very authentic paper form or origami for these models, so the team created a prototype using 6 foot set paper from a local New York paper company. As you can see from the image though, even though the model is relatively simple by origami standards, paper doesn’t stand up when models are folded of this size. So in order to create a pig that would stand up properly had a clean professional look, a new prototype was created.
This new pig prototype was made out of foamcore and was also divided up into sections and panels instead of being folded with traditional origami methods. It was exactly what the client was looking for even if they didn’t know it at first. It did present a new problem however, as now the materials would need to be made with a CNC machine and also custom painted to get the exact color they were going for. This material would also be much better at withstanding the rigors of cross country shipping.
Once the sizes and materials and colors were all finalized, the parts started to roll into the Brooklyn studio, and assembly began.
The staff (here headed by Frank Ling the Senior Artist who designed the foamcore version of the pig) worked over the course of 2 weeks to score, cut, glue, hammer, screw, nail, tape and build the final pig models.
Here is a finished pig with clamps on to help all of the glued parts dry. The smaller pigs took about an hour to create from start to finish and the larger ones took up to 2-3 hours each.
After the completion of the pig assembly, there was another large hurdle to overcome, which was packaging and boxing all of the enormous models. In the end a system of plastic sleds and cardboard support frames were also designed and created to keep the models safe. This was especially important for the many corners of the model that Taro’s needed to make sure wouldn’t get crushed in shipping.
At the end of the process the studio itself was completely covered in packed pig boxes. So much so in fact that the team had to plan out a pathway when they where placing each new box so as not to block themselves into the studio.
Finally a large FedEx delivery was scheduled and all of the pigs were sent on their different ways- some to California, some to New York, some to Vancouver, and some to Toronto. In the end the Taro’s staff was able to visit the Lower Manhattan locations of some of the pigs and see all of them in action. Here’s a glimpse at what they looked like displayed in the store.